Two of the most well-known procedures in the fabrication of machine parts are CNC turning and CNC milling. In fact, these procedures work very differently and relate to more particular types of work.
CNC turning, for instance, is used to create parts that are round or cylindrical in shape. CNC milling is ideal for making parts that have flat surfaces, grooves, or holes.
But beyond just making parts, they play an important role in how quickly and affordably things get done.
It’s important to grasp an idea over how they affect production time and costs to help businesses make better decisions.
CNC Turning: Time-Saving Benefits
CNC turning is a process that spins the material at hand while a cutting tool shapes it. This is very fast for creating round or cylindrical shapes. If you need pipes, rods, or bolts, turning can produce them quickly, with the desired shapes. The material keeps uniformly circulating under the tool, which is characteristic for high-speed production.
Because of its speed, turning is often preferred for simple, symmetrical designs. It reduces the time needed to produce multiple identical parts. This is especially useful for industries that require a large number of the same components, like automotive or plumbing.
CNC Milling and Its Efficiency
CNC milling is a process where the cutting tool moves to shape the material. It’s great for creating parts with flat surfaces, slots, or intricate designs. Because of this versatility, it can handle complex jobs in a single setup. This reduces the time spent on switching tools or repositioning materials.
However, for shapes that are less complex, milling is generally a slower process in comparison to turning. The tool must be fed slowly into the material to maintain the accuracy of the end product. The time taken is proportional to the level of detail in the design.
In several cases, however, milling often avoids some of the essential post-operation steps. It does save time for parts that possess more complexity.
Cost Efficiency in CNC Processes
The difference lies in the way that milling and turning help reduce overall production costs. Millings may take a little bit longer in the process, but they diminish the following steps. This means less tooling, less scrap material, and better precision. Over time, these savings add up, especially for intricate designs.
In contrast, turning is cost-effective in terms of speed. The faster parts are made, the less money is spent on machine time. This makes turning a smart choice for producing large quantities of simple parts. Waste of materials is reduced by the process itself; as it only removes what is necessary to achieve the desired shape.
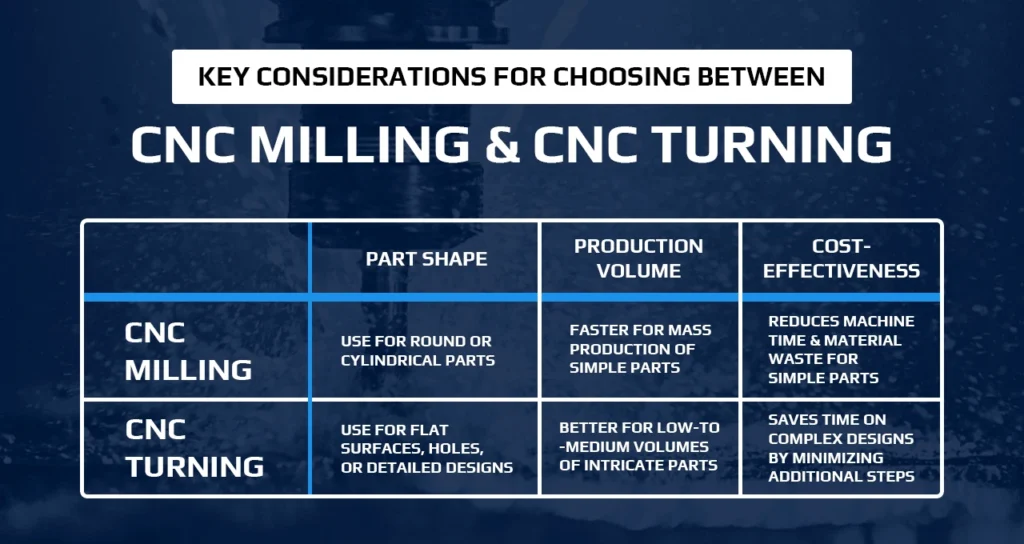
Selecting the Appropriate Process
In many instances, the decision for milling or turning is typically differentiated in the form of the part. Milling will be a suitable process for flat surfaces, holes, and fine detailing in the part. This also polishes off very complex designs and provides extremely precise results.
When it comes to round or cylindrical parts, machining them through turning is more practical. It’s faster and more productive for simple forms. In a nutshell, the low cost of this process ensures quick production times.
Bottom Line
Createproto Rapid System Limited is a leading company, specializing in offering top-notch CNC machining services.
We use state-of-the-art technology including custom CNC milling and turning, 4-, and 5-axis CNC milling, Swiss CNC machining, and metal fabrication services. All of our cutting-edge tools are ISO 9001:2015 certified.
Working with us is very easy!
Select a manufacturing process like custom CNC milling or CNC turning and upload a 2D or 3D drawing. Just after that, you will get the best designs for machining your plastic parts or metal ones. And, you will get real-time pricing just within a few hours. After that the manufacturing process begins and you will receive those parts within 5 days.
Visit our Instagram Page today! If you have any queries, call us now!